There are occasional posts here in the forum asking for info on hand pushing, but there doesn't seem to be much out there. I'm a handpiece guy for many reasons, but I was an old school hammer & chisel and hand push guy back in the day, so I thought I'd look into this.
I've been experimenting with the EG105 gravers for hand pushing using what's often referred to as a European style heel. I've seen this heel geometry in America 30+ years ago so I don't really know it's true origin, but it's often referred to as European.
To achieve this heel with the EasyGraver fixture, I simply sharpened the heel about 20x longer than I normally would. Obviously there will be some heel drag with this geometry, but it works well for hand pushing when my normal micro-short heel does not.
I'm the first to admit I'm really rusty with hand pushing, but here's a shot of my test with the large heel EG105 graver.
I've also made up a EG120 with large heel and I just started testing that one as well. From what I can see it performs similarly.
This is definitely an option for those wanting an inexpensive way into hand engraving.
Martin Strolz has an excellent post on a similar graver geometry in the Tips Archive which got me motivated to do some research.
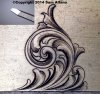
I've been experimenting with the EG105 gravers for hand pushing using what's often referred to as a European style heel. I've seen this heel geometry in America 30+ years ago so I don't really know it's true origin, but it's often referred to as European.
To achieve this heel with the EasyGraver fixture, I simply sharpened the heel about 20x longer than I normally would. Obviously there will be some heel drag with this geometry, but it works well for hand pushing when my normal micro-short heel does not.
I'm the first to admit I'm really rusty with hand pushing, but here's a shot of my test with the large heel EG105 graver.
I've also made up a EG120 with large heel and I just started testing that one as well. From what I can see it performs similarly.
This is definitely an option for those wanting an inexpensive way into hand engraving.
Martin Strolz has an excellent post on a similar graver geometry in the Tips Archive which got me motivated to do some research.
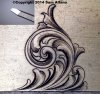