Barry Lee Hands
~ Elite 1000 Member ~
When I was in Japan a couple of years ago I met Katsuo Kato and his son Masafumi Kato, the 25th and 26th generation Kanefusa Fujiwara sword makers.
Here are some pics of them , the assistants Hiroaki Fukudome and Hiroaki Korogi, and myself.
They demonstrated their swordmaking to me and showed me the engraving block and chisels used in their work.
Katso Kato and I in front of his forge in his workshop in Seki city.
One of the assistants with raw steel ready to be forged into a billet
What becomes of the steel when finished forging
A heated billet
Forging
Now the lookeylou gets to try
try harder
Not as easy as it looks
Here are some pics of them , the assistants Hiroaki Fukudome and Hiroaki Korogi, and myself.
They demonstrated their swordmaking to me and showed me the engraving block and chisels used in their work.
Katso Kato and I in front of his forge in his workshop in Seki city.
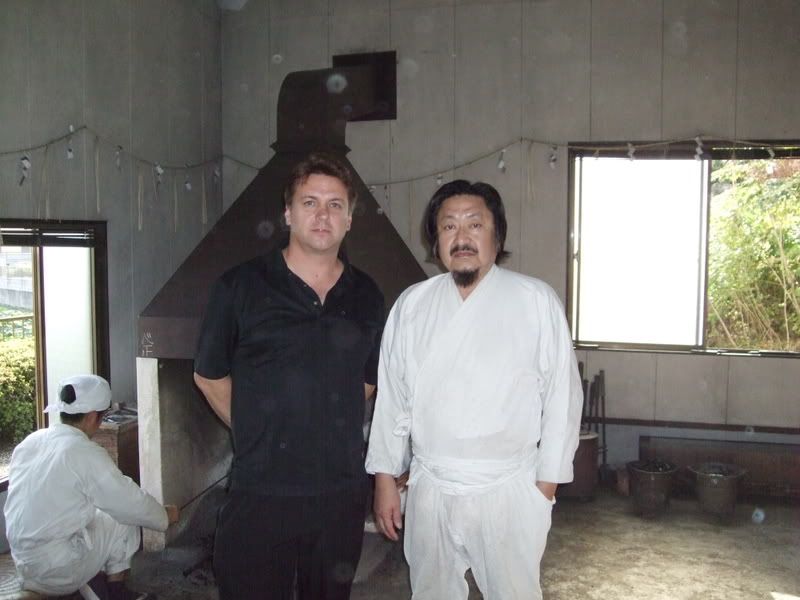
One of the assistants with raw steel ready to be forged into a billet
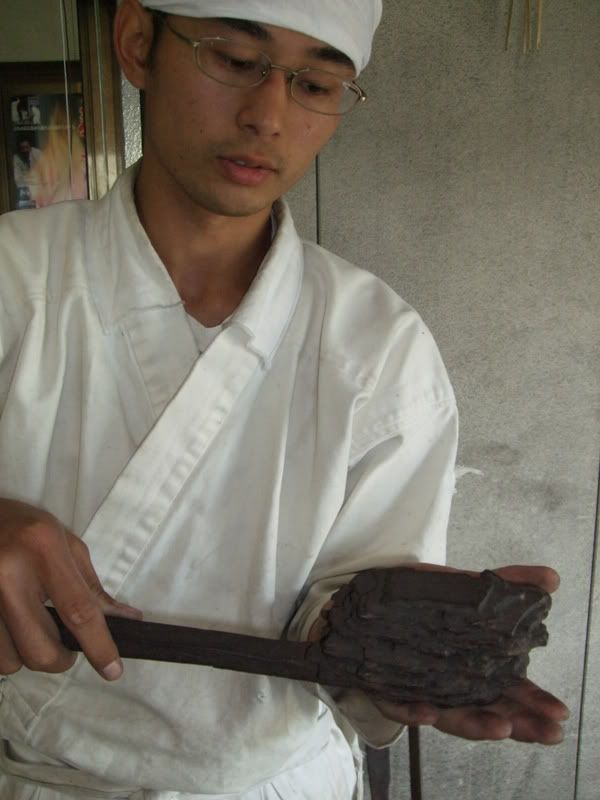
What becomes of the steel when finished forging
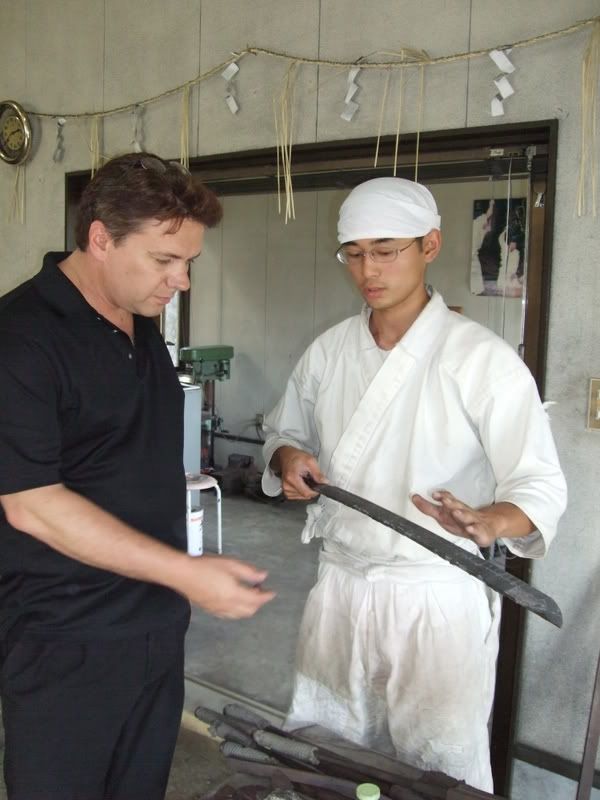
A heated billet
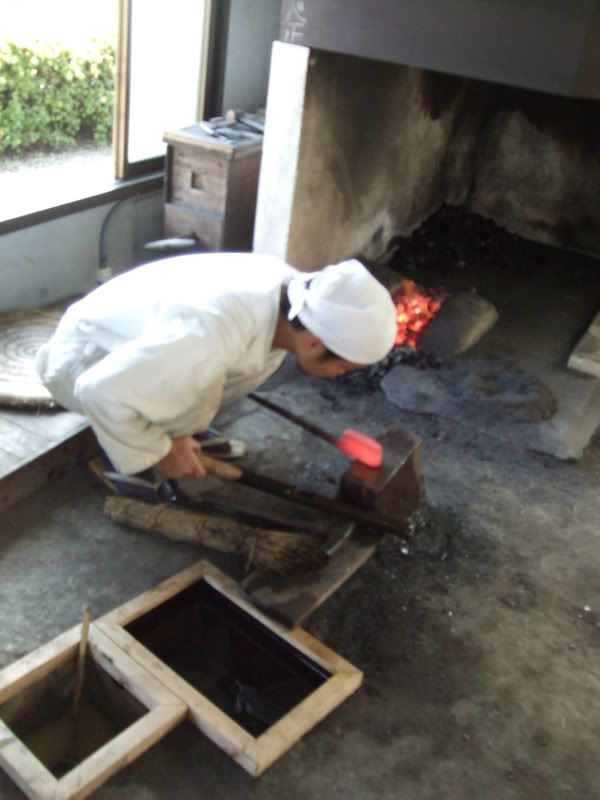
Forging
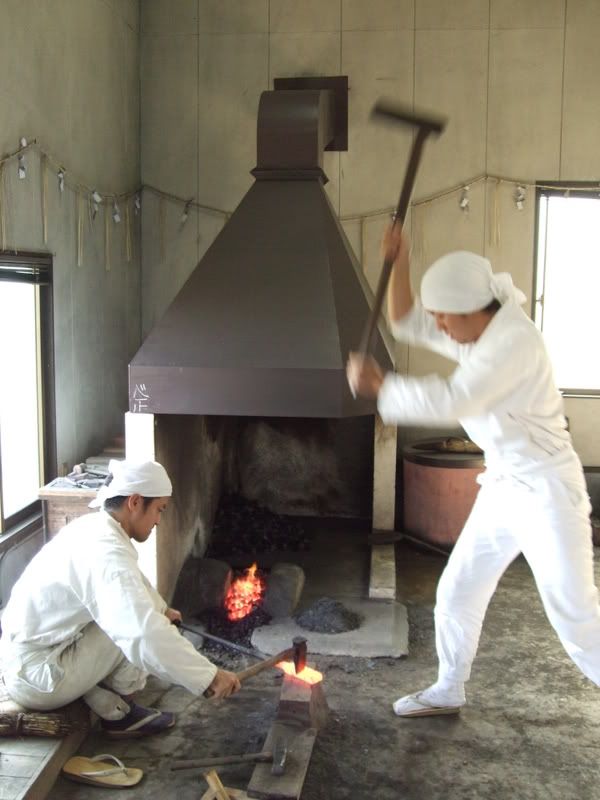
Now the lookeylou gets to try
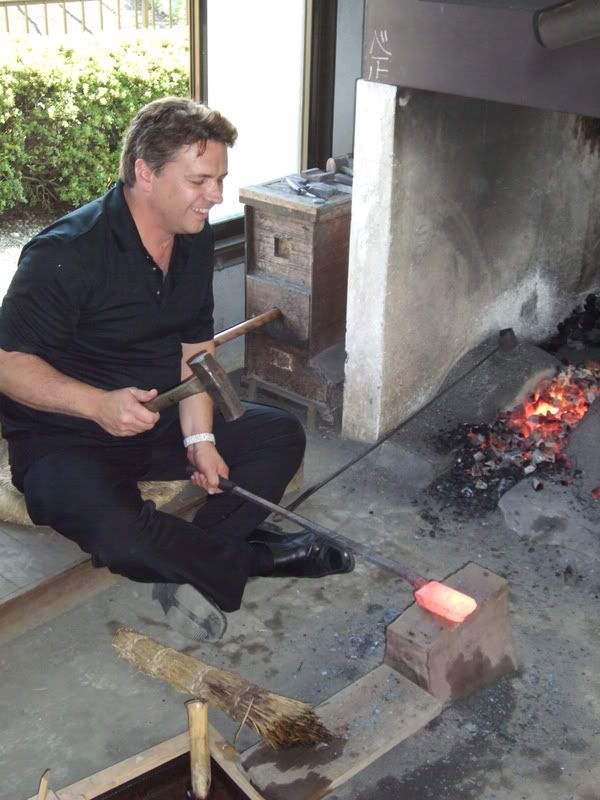
try harder
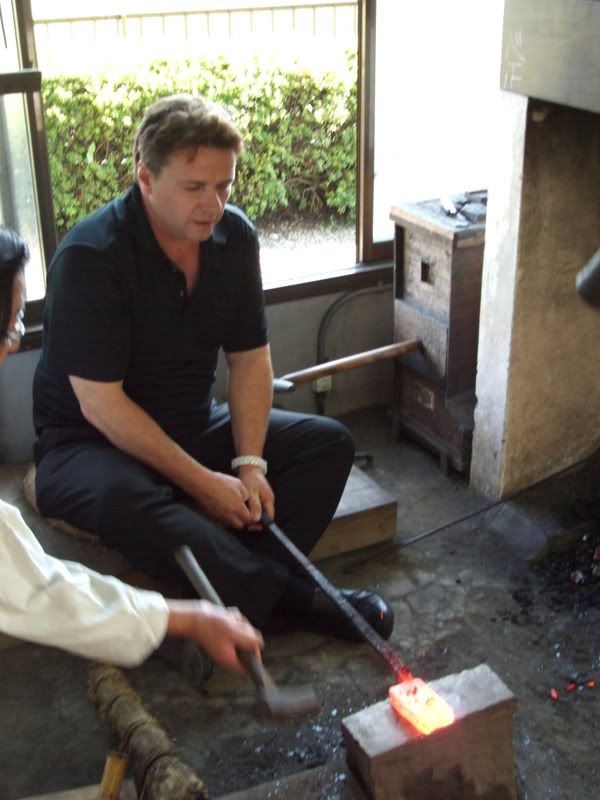
Not as easy as it looks
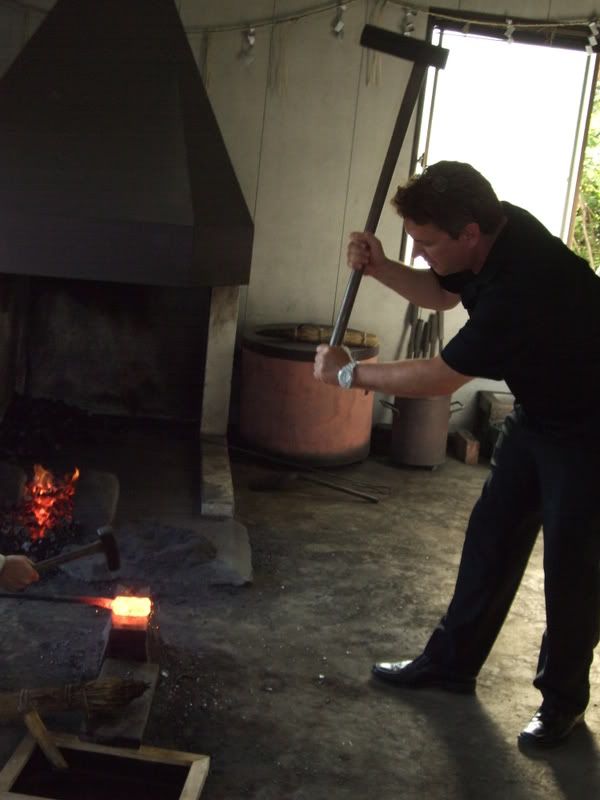
Last edited: