tsterling
Elite Cafe Member
Hi Folks,
Sorry I haven’t been posting much lately, but here’s my latest knife. It’s a tiny deer antler Orca done in NW Native American style.

The knife is 3 3/16 inches overall, with a 1 1/4 inch long 1074 carbon steel through-tang blade. The antler has been aged with potassium permanganate. The handle is made from the last fork of a really old (and tiny) naturally-shed antler.
I’ve been experimenting with engraving and carving antler lately, and have come up with a combination of engraving the edges/outlines with a Lindsay template onglette, carving out the background spaces with NSK and carbide burs, followed by some special little scrapers I’ve made. Tiny flats help on occasion as well. Seems to work fairly well. You do need to take fairly small repeated cuts with the onglette, or the surface of the antler can tear. With small cuts there is still some tearing out, but it’s microscopic and doesn’t seem to hurt the finished product viewed by the naked eye.
I was sort of surprised, because under the microscope carving antler at this tiny scale reminds me very much of carving ivory soap! What seems hard and unyielding with a standard knife is gentle and easy with tiny tools.
Anyway, it’s good to be back, and thanks for looking!
Tom
Sorry I haven’t been posting much lately, but here’s my latest knife. It’s a tiny deer antler Orca done in NW Native American style.

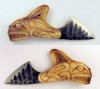
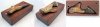
The knife is 3 3/16 inches overall, with a 1 1/4 inch long 1074 carbon steel through-tang blade. The antler has been aged with potassium permanganate. The handle is made from the last fork of a really old (and tiny) naturally-shed antler.
I’ve been experimenting with engraving and carving antler lately, and have come up with a combination of engraving the edges/outlines with a Lindsay template onglette, carving out the background spaces with NSK and carbide burs, followed by some special little scrapers I’ve made. Tiny flats help on occasion as well. Seems to work fairly well. You do need to take fairly small repeated cuts with the onglette, or the surface of the antler can tear. With small cuts there is still some tearing out, but it’s microscopic and doesn’t seem to hurt the finished product viewed by the naked eye.
I was sort of surprised, because under the microscope carving antler at this tiny scale reminds me very much of carving ivory soap! What seems hard and unyielding with a standard knife is gentle and easy with tiny tools.
Anyway, it’s good to be back, and thanks for looking!
Tom