Barry Lee Hands
~ Elite 1000 Member ~
I posted this over on the engraving forum and thought you might like to see it. I used the Lindsay Artisan foot contol tool for most of it. The Artisan is designed for jewelers but works quite well for gun engraving, and its a pretty simple and inexpensive setup. I have the optional Tungsten piston in mine for heavier work, and the standard piston for lighter work.
1 Here are the parts and a photo I took of a mounted Elk.
2 Next the Elk is scribed on with a pantograph, then modified for artistic merit with a scribe. Then I cut the outline with the Lindsay Artisan handpiece.
3 Next I scanned the outline which I cut and put the floorplate and the printed scan on the Pantograph to get the ratios correct so I can scribe it as I cut it, onto the gold.
4 Then pantograph it on the 24k gold.
5 After that I cut a line around it to give the jewelers saw an easy path to follow.
6 Next saw it out.
7 ready to be damascened.
8 raising a burr field inside the outline of the Elk.
9 The gold is annealed.
10 I punch the Elk down, started at the farthest points, the antler tips etc, and work my way in, hammering away.
11 all punched down, next it is sanded with 600 grit backed by a rubber block.
12 The Bulino is begun using a 70 degree tool with a lot of draft.
13 the scrolls are laid out.
14 the scrolls are cut.
15 the leaves are cut
16 The backgound behind the elk is blasted with aluminum oxide.
17 Finished.
18 The finished floorplate and triggerguard.
1 Here are the parts and a photo I took of a mounted Elk.
2 Next the Elk is scribed on with a pantograph, then modified for artistic merit with a scribe. Then I cut the outline with the Lindsay Artisan handpiece.
3 Next I scanned the outline which I cut and put the floorplate and the printed scan on the Pantograph to get the ratios correct so I can scribe it as I cut it, onto the gold.
4 Then pantograph it on the 24k gold.
5 After that I cut a line around it to give the jewelers saw an easy path to follow.
6 Next saw it out.
7 ready to be damascened.
8 raising a burr field inside the outline of the Elk.
9 The gold is annealed.
10 I punch the Elk down, started at the farthest points, the antler tips etc, and work my way in, hammering away.
11 all punched down, next it is sanded with 600 grit backed by a rubber block.
12 The Bulino is begun using a 70 degree tool with a lot of draft.
13 the scrolls are laid out.
14 the scrolls are cut.
15 the leaves are cut
16 The backgound behind the elk is blasted with aluminum oxide.
17 Finished.
18 The finished floorplate and triggerguard.
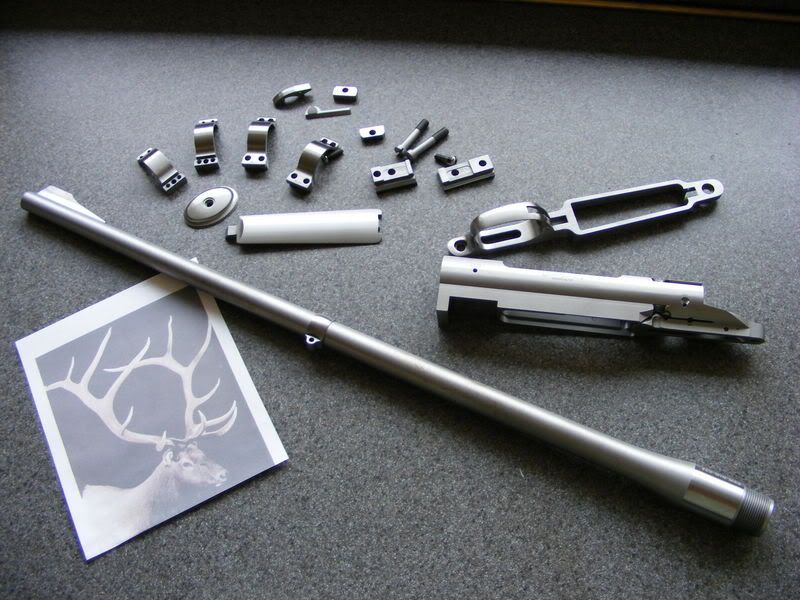
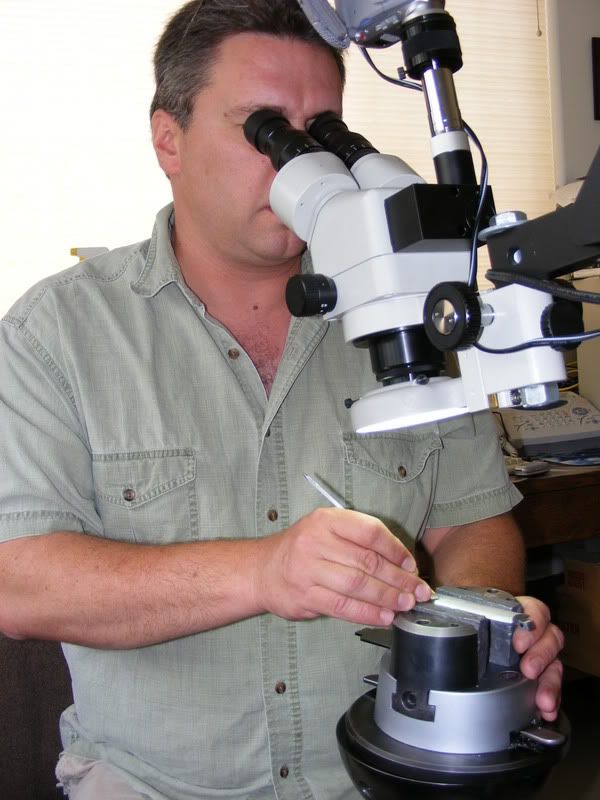
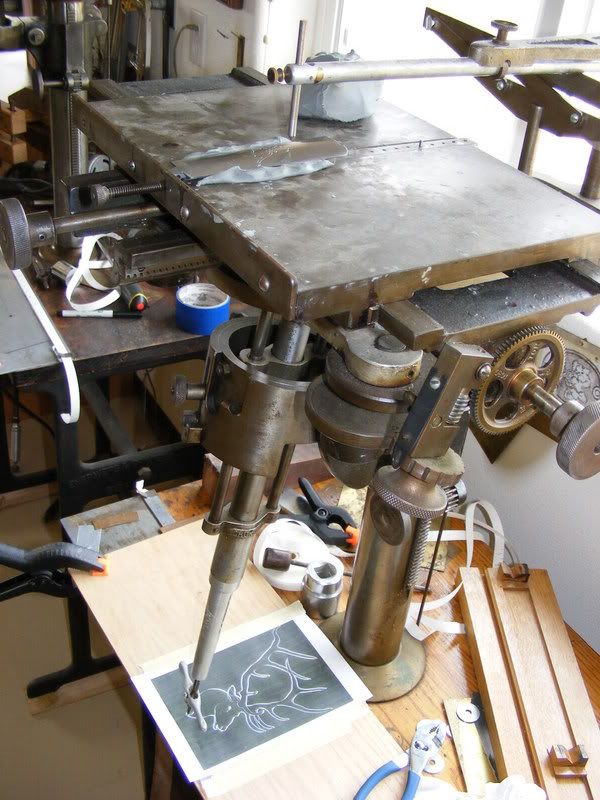
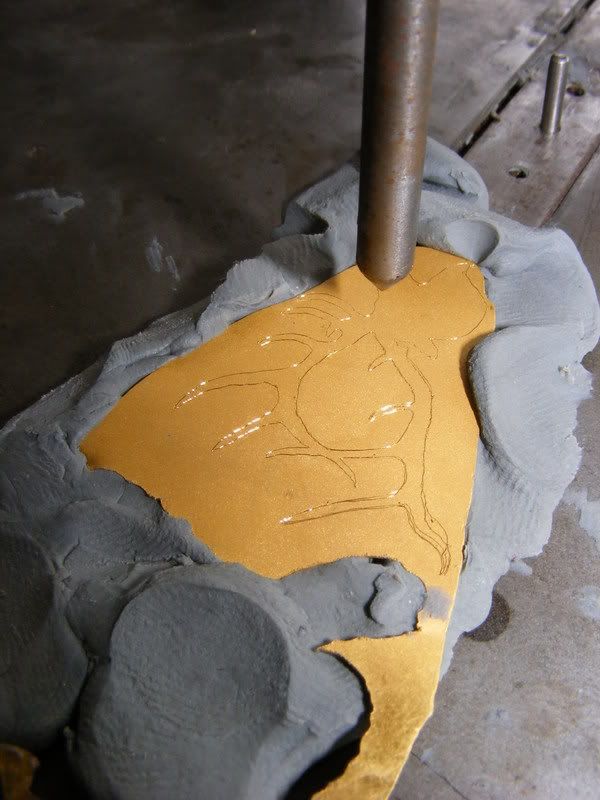